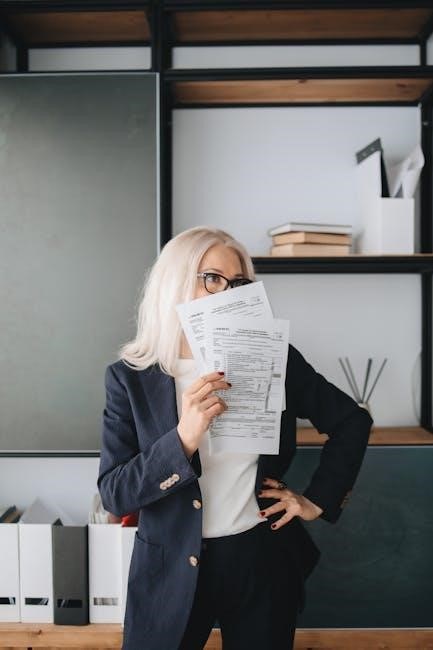
ipc 620b pdf
IPC-620B is the industry-standard specification for cable and wire harness assemblies, ensuring quality and reliability in manufacturing. Developed collaboratively by IPC and WHMA, it provides critical guidelines for acceptance criteria, addressing technical requirements and best practices for the production of wire harnesses. This standard is widely adopted across industries, promoting consistency and excellence in assembly processes.
Overview of IPC-620B
IPC-620B is a widely recognized standard for the requirements and acceptance of cable and wire harness assemblies. Developed by IPC and the Wire Harness Manufacturers Association (WHMA), this document serves as a critical guide for manufacturers, ensuring high-quality production. It outlines essential criteria for materials, workmanship, and inspection, providing a comprehensive framework for assembly processes. The standard is designed to promote consistency and reliability across the industry, making it a vital resource for companies involved in cable and wire harness manufacturing. Its detailed specifications and guidelines help manufacturers meet customer expectations and maintain compliance with industry standards. IPC-620B is regularly updated to reflect advancements in technology and industry practices, ensuring its relevance in an evolving manufacturing landscape.
History and Development
IPC-620B was developed through a collaborative effort between the Institute for Printed Circuits (IPC) and the Wire Harness Manufacturers Association (WHMA). First released in 2002, the standard has undergone several revisions to address evolving industry needs. The “B” revision, published in 2012, introduced significant updates, including enhanced technical specifications and improved clarity. This revision was the result of extensive feedback from industry experts and manufacturers, ensuring the standard aligns with modern manufacturing practices. IPC-620B is now recognized as the benchmark for cable and wire harness assemblies, with periodic updates to reflect technological advancements and industry demands. Its development reflects a commitment to fostering quality and innovation in the electronics manufacturing sector.
Importance of IPC-620B in the Industry
IPC-620B plays a pivotal role in ensuring the quality and reliability of cable and wire harness assemblies across various industries. By establishing standardized acceptance criteria, it minimizes variability in production, leading to higher product consistency and reduced defects. This standard is particularly crucial in sectors where failure of electrical systems can have severe consequences, such as aerospace, automotive, and industrial equipment manufacturing. Compliance with IPC-620B enhances a company’s credibility and competitiveness, as it demonstrates adherence to industry best practices. Furthermore, it facilitates smoother communication between manufacturers and customers, ensuring that products meet specified requirements. The widespread adoption of IPC-620B underscores its importance as a cornerstone of quality assurance in modern manufacturing processes.
Key Features and Updates
IPC-620B introduces enhanced technical specifications, improved ease of use, and compatibility with other assembly standards, ensuring alignment with modern manufacturing needs and industry advancements.
New Additions in IPC-620B Revision
The IPC-620B revision incorporates significant updates, including new sections on advanced materials and manufacturing techniques. It expands criteria for high-reliability applications, such as aerospace and defense, ensuring assemblies meet stringent performance demands. Additional emphasis is placed on automation and robotics integration, aligning with Industry 4.0 trends. The revised standard also introduces updated visual inspection guidelines, incorporating digital tools for enhanced accuracy. Furthermore, there are new provisions for environmental and sustainability considerations, reflecting industry shifts toward greener practices. These additions aim to address evolving industry needs, ensuring the standard remains relevant and comprehensive for modern wire harness manufacturing.
Technical Updates and Enhancements
IPC-620B introduces enhanced technical specifications, improving clarity and precision for cable and wire harness assemblies. Key updates include revised criteria for soldering, crimping, and insulation, ensuring higher reliability. New test methods for conductivity and durability have been added, addressing modern material advancements. The standard also incorporates updated tables and figures for better visualization of acceptance criteria. Additionally, it aligns with emerging technologies, such as automated inspection systems and smart manufacturing practices. These updates reflect industry feedback, focusing on addressing common challenges and improving manufacturability. The enhanced technical guidelines ensure assemblies meet rigorous quality standards, supporting applications in demanding environments like aerospace and automotive industries. These changes underscore IPC’s commitment to advancing manufacturing excellence.
Improved Ease of Use and Compatibility
IPC-620B has been refined to enhance usability, making it more accessible for manufacturers and inspectors. The updated standard integrates seamlessly with other industry specifications, ensuring compatibility and reducing conflicts. New visual aids, such as detailed diagrams and tables, clarify complex requirements, aiding in interpretation. Additionally, the standard now aligns with modern manufacturing systems, including automated inspection tools, streamlining workflows. Compatibility with emerging technologies and software solutions further supports its adaptability. These improvements make IPC-620B a user-friendly resource while maintaining its rigorous quality standards. Enhanced cross-referencing and indexing also simplify navigation, allowing professionals to quickly locate relevant information. Overall, these updates ensure the standard remains practical and efficient for diverse applications across industries.
Requirements and Acceptance Criteria
IPC-620B outlines detailed requirements for cable and wire harness assemblies, including visual inspection, mechanical integrity, and electrical performance standards to ensure product quality and reliability.
Visual Inspection Requirements
IPC-620B specifies rigorous visual inspection criteria for cable and wire harness assemblies to ensure compliance with industry standards. Inspectors must verify the integrity of wires, connectors, and solder joints, checking for damage, misalignment, or improper crimping. The standard details acceptable and unacceptable conditions, such as wire abrasion, insulation breaches, or terminal over-crimping. Visual inspections also cover labeling accuracy, routing, and securing of harnesses. High-magnification tools may be used to examine solder joints and connections. Documentation of findings is mandatory, with clear pass/fail criteria. These requirements ensure assemblies meet quality benchmarks, reducing the risk of defects and ensuring reliability in final products. Proper training and certification of inspectors are critical to maintaining consistency in visual inspections across manufacturing environments.
Mechanical Testing Parameters
IPC-620B outlines specific mechanical testing parameters to ensure the durability and reliability of cable and wire harness assemblies. These tests include pull tests for connectors and crimp joints, verifying they meet minimum force requirements, typically 10N for crimps. Torque tests for connectors ensure proper mating forces without damage. Insulation resistance testing checks for electrical isolation, with standards requiring a minimum of 0.1kΩ to 100MΩ at 500VDC. Tensile strength and flexure tests assess the harness’s ability to withstand mechanical stress. These parameters ensure assemblies can endure environmental and operational strains, maintaining performance and safety. Compliance with these tests is critical for meeting industry standards and delivering reliable products. Proper documentation of test results is essential for quality assurance and traceability in manufacturing processes.
Electrical Testing Standards
IPC-620B establishes rigorous electrical testing standards to ensure the integrity and reliability of cable and wire harness assemblies. Key tests include insulation resistance, dielectric strength, and continuity verification. Insulation resistance testing is typically conducted at 500VDC, with minimum acceptable values ranging from 0.1kΩ to 100MΩ, depending on the application. Dielectric strength tests assess the withstand voltage between conductors and shields, ensuring no breakdown occurs under specified voltages. Continuity testing confirms proper connections, while voltage drop tests verify signal integrity. These standards ensure assemblies meet safety and performance requirements, preventing electrical failures in harsh environments. Compliance with these tests is crucial for maintaining product reliability and meeting industry standards. Proper documentation of electrical test results is essential for quality assurance and traceability in manufacturing processes.
Documentation and Record-Keeping
IPC-620B emphasizes the importance of thorough documentation and record-keeping to ensure compliance and traceability throughout the manufacturing process. Detailed assembly drawings, work instructions, and inspection records must be maintained for each wire harness assembly. Test results, including electrical and mechanical inspections, should be documented and archived. Material certifications, such as those for wires, connectors, and insulation, must also be retained. Proper documentation ensures that all assemblies meet specified requirements and facilitates quality audits. Additionally, records should include lot numbers, serialization, and production dates to enable traceability. This level of documentation supports defect analysis and corrective action processes, ensuring continuous improvement and adherence to industry standards. Accurate and comprehensive records are essential for maintaining quality, safety, and customer satisfaction in wire harness manufacturing.
Industry Applications
IPC-620B is widely applied across industries requiring reliable cable and wire harness assemblies, including aerospace, automotive, telecommunications, and industrial equipment manufacturing, ensuring high-quality standards.
- Aerospace and defense for mission-critical systems.
- Automotive manufacturing for vehicle electrical systems.
- Telecommunications for network infrastructure.
- Industrial equipment for durable and precise connections.
Aerospace and Defense
IPC-620B plays a critical role in the aerospace and defense industries, where high-reliability cable and wire harness assemblies are essential for mission-critical systems. The standard ensures that harnesses withstand the harsh environments often encountered in aerospace applications, such as extreme temperatures, vibrations, and exposure to hazardous materials. By adhering to IPC-620B, manufacturers can produce assemblies that meet strict regulatory and safety requirements, ensuring the integrity of electrical systems in aircraft, spacecraft, and defense equipment. This is particularly important for applications where failure could result in significant operational risks or safety hazards. The standard’s rigorous testing and inspection criteria help maintain the performance and reliability of these systems, making it a cornerstone of quality assurance in the sector.
Automotive Manufacturing
IPC-620B is instrumental in automotive manufacturing, where high-quality cable and wire harness assemblies are crucial for vehicle reliability and safety. The standard ensures that harnesses meet rigorous performance requirements, particularly in harsh automotive environments. With the increasing reliance on advanced electronics in modern vehicles, IPC-620B provides clear guidelines for manufacturing cable assemblies that can withstand vibrations, temperature fluctuations, and other stresses. By adhering to IPC-620B, automotive manufacturers can ensure the durability and performance of electrical systems, reducing the risk of failure. The standard also aligns with industry demands for consistency and quality, making it a vital tool for maintaining competitiveness in the automotive sector. Its implementation supports the production of safe and reliable vehicles, addressing the evolving needs of the industry.
Industrial Equipment
IPC-620B plays a vital role in the manufacturing of industrial equipment, where reliable cable and wire harness assemblies are essential for operational efficiency. The standard provides detailed acceptance criteria for harnesses used in heavy machinery, robotics, and control systems, ensuring durability and performance in harsh industrial environments. By adhering to IPC-620B, manufacturers can minimize downtime and ensure the safety of equipment operation. The standard also addresses critical aspects such as power distribution, signal integrity, and resistance to environmental factors like temperature and vibration. This makes IPC-620B a cornerstone for producing high-quality cable assemblies that meet the demanding requirements of industrial applications. Its implementation supports the reliability and longevity of industrial equipment, aligning with the need for consistent quality and global standards.
Telecommunications
IPC-620B is instrumental in the telecommunications industry, where reliable cable and wire harness assemblies are critical for maintaining signal integrity and network performance. The standard ensures the quality of connections in communication systems, from data centers to fiber-optic networks. Its guidelines are essential for preventing signal loss, electromagnetic interference, and other issues that could compromise data transmission. By adhering to IPC-620B, manufacturers can produce harnesses that meet the stringent requirements of the telecom sector, ensuring high-speed data transfer and system reliability. The standard also supports the development of scalable and flexible network infrastructures, enabling telecom companies to deliver consistent and high-quality services globally. This makes IPC-620B a cornerstone for advancing telecommunications technology and maintaining its operational excellence;
Certification and Training
IPC offers certification programs for professionals, ensuring expertise in IPC-620B standards. Training programs provide in-depth knowledge on cable and wire harness assembly requirements, enhancing industry skills and compliance.
IPC Certification Programs
IPC certification programs are designed to validate expertise in IPC-620B standards, focusing on cable and wire harness assembly requirements. These programs ensure professionals understand and apply the guidelines effectively, fostering industry compliance and quality; Training modules cover visual inspection, mechanical testing, and documentation, preparing individuals to meet the rigorous standards of the industry. By participating in these programs, professionals gain the knowledge and skills needed to produce high-quality assemblies, aligning with the latest revisions and updates in the IPC-620B specification. This certification is recognized globally, enhancing career opportunities and contributing to the advancement of manufacturing excellence.
Training for Professionals
Training for professionals on IPC-620B focuses on enhancing skills in cable and wire harness assembly, ensuring adherence to industry standards. These programs cover visual inspection, mechanical testing, and documentation, providing hands-on experience with the latest tools and techniques. Professionals learn to identify defects, perform precise measurements, and maintain thorough records, all aligned with IPC-620B requirements. The training emphasizes practical application, enabling participants to implement best practices in real-world scenarios. By completing these courses, professionals can improve product quality, reduce errors, and contribute to a more efficient manufacturing process. Such training is essential for staying competitive and meeting the evolving demands of the industry, ensuring that professionals are well-equipped to handle complex assembly challenges effectively.
Compliance and Quality Assurance
Compliance with IPC-620B ensures assemblies meet rigorous quality standards through visual inspections, mechanical testing, and precise documentation. These processes guarantee reliability and adherence to industry requirements, fostering trust and consistency in manufacturing practices.
Ensuring Compliance with IPC-620B
Ensuring compliance with IPC-620B involves rigorous adherence to its guidelines for cable and wire harness assemblies. This includes conducting thorough visual inspections, performing mechanical and electrical tests, and maintaining detailed documentation. Manufacturers must implement quality assurance processes to verify that all assemblies meet the standard’s criteria. Training personnel on IPC-620B requirements and utilizing certified inspection tools are critical steps. Regular audits and continuous improvement practices help maintain compliance and address any deviations promptly. By following these measures, companies can ensure their products meet industry standards, enhancing reliability and customer satisfaction in various sectors such as aerospace, automotive, and telecommunications. Compliance fosters trust and consistency in manufacturing processes.
Quality Assurance Processes
Quality assurance processes are essential for maintaining adherence to IPC-620B standards. These processes involve systematic inspections, testing, and documentation to ensure compliance. Manufacturers must implement robust quality control measures, including visual inspections, mechanical testing, and electrical verification. Documentation of all test results and assembly processes is critical for traceability and accountability. Regular audits and corrective action plans help identify and resolve defects promptly. Additionally, employee training and certification programs ensure that staff are well-versed in IPC-620B requirements. By integrating these practices, companies can uphold consistent quality, reduce defects, and improve customer satisfaction. Quality assurance processes also facilitate continuous improvement, ensuring that products meet the highest industry standards for reliability and performance.
Challenges and Solutions
Implementing IPC-620B often presents challenges like complex requirements and training needs. Solutions include comprehensive training programs and leveraging industry tools to ensure compliance and quality.
Common Implementation Challenges
Implementing IPC-620B can present several challenges, including understanding complex technical requirements, ensuring proper training for staff, and maintaining consistency across production lines. Additionally, staying updated with the latest revisions and integrating the standard with existing quality systems can be difficult. Many organizations struggle with interpreting acceptance criteria and applying them uniformly. Another challenge is managing documentation and record-keeping requirements, which are critical for compliance. Furthermore, the standard’s emphasis on visual inspection and testing can strain resources for smaller manufacturers. Addressing these challenges requires a structured approach to training, process optimization, and leveraging industry resources to ensure successful implementation and compliance with IPC-620B standards.
Best Practices for Overcoming Obstacles
To overcome challenges in implementing IPC-620B, organizations should adopt a structured approach, starting with comprehensive training programs for staff. Investing in IPC certification courses ensures a standardized understanding of the requirements; Leveraging industry-specific tools and software can streamline compliance and documentation processes. Regular audits and quality checks help maintain consistency and identify gaps early. Collaboration between departments, such as engineering and production, is crucial for aligning processes with the standard. Additionally, staying informed about updates and revisions through official IPC resources and workshops can prevent compliance issues. By fostering a culture of continuous improvement and leveraging best practices, companies can effectively navigate obstacles and achieve successful IPC-620B implementation.
Future Trends and Updates
Future updates to IPC-620B will focus on emerging technologies, automation, and sustainability. Industry collaboration will drive enhancements, ensuring the standard remains relevant and adaptable to evolving manufacturing needs.
Emerging Trends in Wire Harness Manufacturing
The wire harness manufacturing industry is evolving rapidly, with emerging trends like automation, miniaturization, and the use of advanced materials. Automation is streamlining production processes, reducing errors, and improving efficiency. Miniaturization of components is driving demand for smaller, lighter, and more complex harnesses. Additionally, the integration of smart technologies, such as IoT and AI, is enabling real-time monitoring and predictive maintenance. Sustainability is also becoming a key focus, with manufacturers adopting eco-friendly materials and practices. These trends are reshaping the industry, pushing manufacturers to innovate and adapt to meet growing demands for high-performance, reliable, and environmentally responsible wire harness solutions.
Anticipated Revisions and Updates
Future revisions of IPC-620B are expected to address emerging technologies and industry demands. Updates may include expanded guidelines for automation in wire harness assembly, as well as new standards for miniaturized and high-density interconnects. There is also a potential focus on sustainability, incorporating eco-friendly materials and processes. Additionally, revisions may align with advancements in IoT and smart manufacturing, ensuring compatibility with cutting-edge technologies. The standard could also see enhanced testing protocols for reliability and durability, particularly for harsh environments. Stakeholders anticipate updates to reflect global market needs, ensuring IPC-620B remains the cornerstone for cable and wire harness manufacturing. These revisions will aim to improve efficiency, reduce complexity, and meet the evolving demands of modern industries.
Resources and Support
Official IPC resources provide comprehensive guides, training programs, and technical support for IPC-620B implementation. Third-party tools and software also offer design, testing, and compliance solutions to enhance efficiency.
Official IPC Resources
The official IPC website offers extensive resources, including the IPC-620B PDF document, training materials, and certification programs. These resources are designed to help professionals understand and implement the standard effectively. The IPC also provides webinars, workshops, and forums where industry experts share insights and best practices. Additionally, the IPC-620B PDF document itself is a comprehensive guide, detailing requirements, acceptance criteria, and technical updates. It serves as the primary reference for manufacturers, ensuring compliance and quality in cable and wire harness assemblies. These official resources are essential for staying updated and ensuring adherence to industry standards.
Third-Party Tools and Software
Beyond official IPC resources, various third-party tools and software support IPC-620B compliance and implementation. These include CAD design software, such as Autodesk and SolidWorks, which aid in creating precise wire harness designs. CAM tools, like Siemens NX, assist in manufacturing planning, ensuring alignment with IPC-620B standards; Quality control software, such as PQ Systems, helps track and document compliance during production. Additionally, ERP systems like SAP integrate IPC-620B requirements into workflow management. Specialized tools for cable harness testing, such as Cirrus Systems, ensure electrical integrity. These solutions streamline processes, enhance accuracy, and support manufacturers in meeting IPC-620B criteria effectively. They are invaluable for optimizing production and maintaining quality standards in cable and wire harness assembly.
IPC-620B remains a cornerstone for ensuring quality and reliability in cable and wire harness assemblies. Its comprehensive guidelines and updates have cemented its role as an essential standard across industries. By adhering to IPC-620B, manufacturers can maintain consistency, reduce errors, and meet customer expectations. As technology advances, the standard continues to evolve, addressing emerging trends and challenges. Staying informed and compliant with IPC-620B is crucial for businesses aiming to deliver high-quality products. Its widespread adoption underscores its importance in driving innovation and excellence in manufacturing. As industries grow, IPC-620B will remain a vital tool for achieving operational efficiency and maintaining global competitiveness.