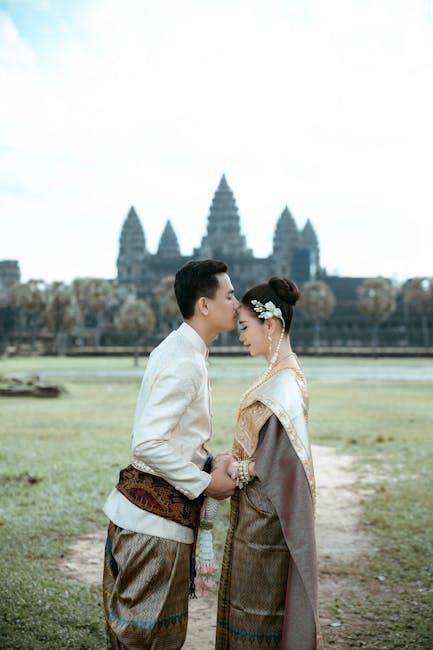
ams2700e pdf
AMS2700E is a specification for passivating corrosion-resistant steels, ensuring removal of contaminants․ It is widely used in aerospace for components, utilizing citric acid for effective passivation․ SAE International governs it․
1․1 Overview of AMS2700E Specification
AMS2700E outlines requirements for passivating corrosion-resistant steels, ensuring removal of free iron and contaminants․ It applies to aerospace components, specifying processes like pickling and passivation․ The document emphasizes surface cleanliness and corrosion resistance, critical for aerospace safety․ Compliance ensures components meet stringent performance standards, addressing material compatibility and process control․ This specification is essential for maintaining the integrity and longevity of steel parts in demanding environments․
1․2 Purpose and Scope of the Document
The purpose of AMS2700E is to establish standardized procedures for passivating corrosion-resistant steels in aerospace applications․ Its scope includes defining processes to remove contaminants, ensuring surface quality, and preventing corrosion․ The document applies to stainless steel components, detailing specific passivation and pickling methods․ It ensures compliance with aerospace material standards, addressing material preparation, bath composition, and testing․ By following AMS2700E, manufacturers achieve consistent, high-quality results, meeting industry requirements for safety and reliability in critical environments․
1․3 Importance of AMS2700E in Aerospace Industry
AMS2700E is crucial in the aerospace industry for ensuring corrosion resistance in stainless steel components․ It provides a standardized method for passivation, enhancing durability and safety in harsh environments․ By adhering to AMS2700E, manufacturers meet stringent aerospace material specifications, reducing the risk of component failure․ The specification is essential for maintaining the structural integrity and longevity of aircraft and spacecraft parts, making it a cornerstone of quality control in the industry․
Key Features of AMS2700E
AMS2700E includes passivation and pickling processes, utilizing citric acid for effective contaminant removal․ It specifies bath composition and parameters to ensure compliance with aerospace standards and material compatibility․
2․1 Passivation and Pickling Processes
AMS2700E outlines detailed passivation and pickling processes to remove contaminants like free iron from corrosion-resistant steel surfaces․ These processes ensure surface purity and corrosion resistance․ Citric acid is commonly used for passivation, offering a non-toxic alternative to nitric acid․ The specification defines immersion steps, rinsing, and drying to achieve optimal results․ Proper passivation enhances material properties, making it critical for aerospace applications where durability and safety are paramount․ Adherence to these processes guarantees compliance with stringent industry standards․
2․2 Material Requirements and Compatibility
AMS2700E specifies material requirements for corrosion-resistant steels, primarily stainless steel alloys․ It ensures compatibility with passivation processes, focusing on removing contaminants without damaging the material․ The specification applies to alloys like 300 series stainless steels but excludes materials with certain coatings or surface finishes․ Compatibility is crucial to achieve optimal corrosion resistance and durability, particularly in aerospace applications where high performance is essential․ Adherence to these requirements guarantees material integrity and reliability in harsh environments․
2․3 Compliance with Aerospace Standards
AMS2700E aligns with stringent aerospace standards, ensuring high-quality passivation processes․ It complements ASTM A967, providing a robust framework for corrosion-resistant steel treatment․ The specification is widely recognized in the aerospace industry for its reliability and adherence to safety protocols; Compliance with AMS2700E guarantees that components meet rigorous performance criteria, essential for critical applications․ This standard is integral to maintaining the integrity and durability of aerospace systems, ensuring they withstand extreme conditions and operational demands effectively․
Application of AMS2700E
AMS2700E is primarily applied in the aerospace and defense industries for passivating corrosion-resistant steel components․ It is used for connectors, fasteners, and other critical hardware, ensuring reliability and durability in harsh environments․
3․1 Industries That Use AMS2700E
AMS2700E is predominantly utilized in the aerospace and defense industries due to its stringent requirements for corrosion-resistant steel components․ It is also applied in manufacturing sectors requiring high precision and durability, such as automotive and medical devices․ The specification ensures compliance with international standards, making it a preferred choice for industries where material reliability is critical․ Its adoption is particularly notable in environments where components are exposed to harsh conditions, necessitating superior corrosion resistance and surface quality․ This versatility underscores its importance across various industrial applications․
3․2 Specific Components Covered by the Specification
AMS2700E primarily addresses the passivation of corrosion-resistant steel components such as fasteners, fittings, and connectors․ It also covers springs, wire, and other small hardware used in aerospace applications; The specification ensures these components meet stringent surface finish and cleanliness requirements․ Additionally, it applies to parts exposed to harsh environmental conditions, requiring enhanced corrosion resistance․ Components fabricated from stainless steel alloys, particularly those used in critical systems, fall under this specification․ Its scope includes both newly manufactured parts and those requiring refurbishment or maintenance, ensuring uniform quality across all applications․
3․3 Role in Corrosion-Resistant Steel Fabrication
AMS2700E plays a pivotal role in corrosion-resistant steel fabrication by outlining processes to remove contaminants like free iron․ This ensures surfaces are clean and resistant to corrosion․ By standardizing passivation and pickling, it enhances material durability and performance in aerospace environments․ Compliance with AMS2700E guarantees components meet rigorous industry standards, reducing corrosion risks and extending service life․ Its methodologies are integral to producing high-quality, reliable steel parts for demanding applications where failure is not an option․ This specification is essential for maintaining structural integrity and safety in critical systems․ Its guidelines are widely adopted across the aerospace industry․
Process Requirements
AMS2700E specifies essential steps for passivation, including bath composition, temperature, and duration․ It ensures proper removal of contaminants and adherence to strict aerospace standards, guaranteeing quality and safety․
4․1 Steps Involved in Passivation
The passivation process under AMS2700E involves several critical steps, including surface cleaning, acid treatment, rinsing, and drying․ Surface cleaning removes grease and oils, while acid treatment dissolves contaminants․ Rinsing ensures no residual chemicals remain, and drying prevents water spots․ These steps are carefully controlled to maintain surface integrity and corrosion resistance, adhering to strict aerospace standards․ Proper sequencing and parameter control are essential for achieving the desired results, ensuring components meet specification requirements for durability and performance in demanding environments․
4․2 Bath Composition and Parameters
The passivation bath typically consists of citric acid solutions, with pH levels carefully controlled between 3․2 and 3․7․ Temperature ranges are maintained between 40°C to 60°C to ensure optimal results․ The bath composition is designed to effectively remove free iron and contaminants without damaging the steel surface․ Water quality and chemical purity are critical to avoid re-contamination․ Strict control of these parameters ensures consistent passivation outcomes, meeting AMS2700E requirements for corrosion resistance and surface finish․ Regular monitoring and adjustments are necessary to maintain bath effectiveness and component quality․
4․3 Quality Control and Testing
Quality control involves rigorous testing to ensure passivation meets AMS2700E standards․ Common tests include copper sulfate to detect free iron and water immersion to check for rust․ Visual inspections verify surface finish and cleanliness․ Chemical analysis ensures bath composition adheres to specifications․ Documentation of test results is mandatory for compliance․ Testing ensures components meet corrosion resistance and surface quality requirements, providing assurance of long-term performance in aerospace applications․ Regular audits and process monitoring further enhance quality control effectiveness․
Compliance and Certifications
AMS2700E ensures aerospace components meet strict quality and safety standards through precise documentation and testing, guaranteeing compliance with aerospace material specifications․
5․1 Relationship with ASTM A967
AMS2700E and ASTM A967 both address passivation of corrosion-resistant steels but serve different industries․ ASTM A967 is broader, covering various steel types and applications, while AMS2700E is tailored for aerospace, emphasizing strict quality and precision․ Both specifications often align in passivation processes, such as using citric acid, but AMS2700E includes additional aerospace-specific requirements․ Manufacturers may comply with both by adhering to AMS2700E’s rigorous standards, ensuring compatibility with aerospace demands while meeting ASTM’s general guidelines for passivation․
5․2 Superseding and Reference Documents
AMS2700E supersedes AMS2700D, issued in 2000 and revised in 2018․ It references key documents like ASTM A967 for passivation standards and ASTM A240 for steel classifications․ These references ensure compliance with established material and process requirements, maintaining consistency across specifications while focusing on aerospace applications․
5․3 Manufacturer Responsibilities
Manufacturers must adhere to AMS2700E specifications, ensuring proper passivation and pickling processes․ They are responsible for maintaining process controls, documenting procedures, and verifying compliance․ Manufacturers must use approved chemicals, such as citric acid, and ensure all steps meet the specification․ Proper training of personnel and equipment calibration are also required․ Final inspection and testing must confirm the product meets all requirements before delivery, ensuring reliability and safety in aerospace applications․ Compliance with these responsibilities is critical to maintaining certification and industry standards․
Technical Specifications
AMS2700E specifies surface finish, contaminant removal, and performance metrics․ It includes citric acid bath parameters and pH levels for effective passivation of corrosion-resistant steels․
6․1 Surface Finish Requirements
AMS2700E specifies surface finish requirements for corrosion-resistant steels, ensuring maximum roughness and cleanliness․ The process involves passivation and pickling to achieve a smooth, contaminant-free surface․ Proper surface preparation is critical to meet aerospace standards․ The specification outlines acceptable roughness levels and methods for removing contaminants․ Citric acid baths are commonly used, with strict pH and temperature controls․ These requirements ensure optimal surface quality, essential for corrosion resistance and durability in aerospace applications․ Compliance with these standards is verified through rigorous testing and inspection processes․
6․2 Contaminant Removal Processes
AMS2700E outlines detailed processes for removing contaminants from steel surfaces, emphasizing the use of citric acid solutions․ The passivation process involves immersing components in a bath with controlled pH levels to dissolve metallic impurities․ Post-treatment includes thorough rinsing with clean water to eliminate residues․ These steps ensure the removal of free iron and other contaminants, enhancing corrosion resistance․ The specification also addresses proper drying procedures to prevent re-contamination․ Compliance with these processes is essential for achieving the desired surface quality and durability in aerospace applications․
6․3 Performance Metrics and Standards
AMS2700E establishes strict performance metrics for passivated steel surfaces, ensuring optimal corrosion resistance and durability․ The specification mandates that treated components meet rigorous standards, including minimal surface roughness and maximal contaminant removal․ Citric acid passivation is emphasized for its effectiveness in achieving these metrics․ Compliance with ASTM A967 further ensures uniform quality․ Performance testing includes visual inspections and corrosion resistance evaluations․ Adherence to these standards guarantees components meet aerospace industry demands for reliability and longevity in harsh environments․ Proper documentation and certification are required to verify compliance with all specified metrics․
Safety and Environmental Considerations
AMS2700E emphasizes safe handling and storage of chemicals, proper waste disposal, and operator safety․ Environmental impact is minimized through regulated processes and responsible waste management practices․
7․1 Handling and Storage of Chemicals
AMS2700E requires strict adherence to safety protocols for handling and storing passivation chemicals․ Proper ventilation, protective equipment, and spill containment measures are essential․ Chemicals must be stored in labeled, compatible containers, away from incompatible materials․ Personal protective equipment (PPE) such as gloves, goggles, and respirators should be worn during handling․ Emergency procedures, including spill response plans, must be in place to minimize risks․ Proper training for personnel ensures safe practices and compliance with environmental regulations, reducing potential hazards and environmental impact․
7․2 Waste Disposal and Environmental Impact
AMS2700E emphasizes environmentally responsible disposal of passivation byproducts․ Chemical waste, including citric acid solutions, must be neutralized and disposed of according to local regulations․ Proper treatment, such as pH adjustment, ensures compliance with environmental standards․ Recycling or controlled discharge methods minimize ecological impact․ Facilities must maintain records of waste management practices to demonstrate adherence to sustainability guidelines․ Regular audits ensure compliance, reducing potential harm to the environment and promoting green manufacturing practices in aerospace applications․
7․3 Operator Safety Precautions
Operators handling AMS2700E processes must wear personal protective equipment (PPE), including gloves, goggles, and respirators, to prevent chemical exposure․ Proper ventilation is essential to avoid inhalation of fumes․ Chemicals must be stored in labeled, sealed containers, and spills should be immediately contained․ Emergency eyewashes and showers should be accessible․ Operators must undergo training on safety protocols and emergency procedures․ Regular health monitoring is recommended to ensure worker safety and compliance with occupational health standards․ Adherence to these precautions minimizes risks associated with passivation processes․
Advantages of AMS2700E
AMS2700E enhances corrosion resistance, improves surface quality, and ensures cost-effectiveness in aerospace applications, making it a critical specification for high-performance steel components․
8․1 Improved Corrosion Resistance
AMS2700E ensures enhanced corrosion resistance by effectively removing free iron and contaminants from steel surfaces․ The passivation process creates a protective oxide layer, reducing the risk of corrosion․ This specification is particularly beneficial for aerospace applications, where high-performance materials are critical․ By adhering to AMS2700E, manufacturers achieve long-term durability and reliability in corrosion-resistant steel components, minimizing maintenance and extending service life in harsh environments․
8․2 Enhanced Surface Quality
AMS2700E ensures enhanced surface quality through precise passivation processes, removing contaminants and imparting a smooth, uniform finish․ This specification promotes a clean, corrosion-free surface, essential for aerospace applications․ The process minimizes surface defects, improving component performance and longevity․ By adhering to AMS2700E, manufacturers achieve consistent surface quality, reducing friction and wear․ This ensures reliability in critical systems, making it a cornerstone for high-performance aerospace components․
8․3 Cost-Effectiveness in Aerospace Applications
AMS2700E ensures cost-effectiveness by optimizing passivation processes, reducing material waste, and extending component lifespan․ Utilizing citric acid for passivation not only meets aerospace standards but also minimizes costs․ This process prevents surface contamination and reduces the need for costly rework․ By ensuring a durable, corrosion-resistant finish, AMS2700E lowers long-term maintenance costs․ Its efficiency makes it a cost-effective solution for manufacturers, balancing high performance with economic benefits in aerospace applications․
Challenges and Limitations
AMS2700E involves complex passivation processes, requiring precise control of bath composition and parameters․ Material compatibility issues and strict monitoring demands can pose challenges for manufacturers․
9․1 Complexity of the Passivation Process
The passivation process under AMS2700E is intricate, requiring precise control of bath composition, temperature, and pH levels․ Citric acid solutions are commonly used, but maintaining optimal operating ranges between 3․2 and 3․7 pH demands careful monitoring․ Additionally, the process involves multiple stages, including pickling and rinsing, which must be meticulously executed to ensure effective removal of contaminants without damaging the material․ This complexity necessitates skilled personnel and advanced equipment to meet stringent aerospace standards, adding to the overall challenge of compliance․
9․2 Material Compatibility Issues
Material compatibility is a critical challenge in the AMS2700E process, as not all corrosion-resistant steels respond uniformly to passivation․ Certain high-alloy steels may exhibit reduced effectiveness or surface degradation when treated with citric acid solutions․ This variability necessitates careful material selection and pre-qualification testing to ensure optimal results․ In aerospace applications, where material integrity is paramount, such compatibility issues can lead to costly rework or component rejection, emphasizing the need for precise process control and material validation․
9․3 Maintenance and Monitoring Requirements
Regular maintenance and rigorous monitoring are essential to uphold the integrity of the AMS2700E passivation process․ Bath solutions must be tested frequently to ensure pH levels and chemical concentrations remain within specified ranges․ Temperature control is critical, as deviations can affect passivation efficiency․ Additionally, operator training and strict adherence to safety protocols are necessary to prevent accidents․ Continuous monitoring of process parameters ensures compliance with aerospace standards, while documentation of maintenance activities aids in traceability and quality assurance․ Proper upkeep minimizes downtime and ensures consistent, high-quality results․
Future Trends and Updates
AMS2700E may adopt emerging passivation technologies and updates for enhanced performance and environmental compliance, ensuring it remains a critical standard in aerospace applications․
10․1 Emerging Technologies in Passivation
Emerging technologies in passivation focus on eco-friendly processes, such as citric acid-based treatments, offering improved corrosion resistance and reduced environmental impact․ Automation and real-time monitoring systems enhance process control and consistency․ Advances in nanotechnology and surface coatings further optimize passivation outcomes․ These innovations align with AMS2700E standards, ensuring high performance while addressing sustainability needs in aerospace applications․
10․2 Expected Revisions in AMS2700E
Future revisions of AMS2700E may include updates to chemical parameters and passivation methods, aligning with advancements in corrosion resistance and environmental sustainability․ Expected changes could involve expanded material compatibility and refined testing protocols to ensure compliance with evolving aerospace standards․ The specification may also incorporate new technologies, such as automated monitoring systems, to enhance process consistency and traceability․ These revisions aim to maintain AMS2700E as a cutting-edge standard for corrosion-resistant steel treatments in critical industries․
10․3 Industry Adaptation to New Standards
The aerospace industry is anticipated to adapt swiftly to new standards within AMS2700E, driven by the need for enhanced corrosion resistance and compliance with stricter environmental regulations․ Manufacturers are expected to invest in updated equipment and training to meet revised specifications․ Collaboration between suppliers and regulatory bodies will be crucial to ensure seamless implementation․ The industry’s proactive approach will maintain its competitive edge, ensuring components meet the highest quality and safety benchmarks while aligning with global aerospace standards and practices․ This adaptation underscores the sector’s commitment to innovation and excellence․
AMS2700E is crucial for ensuring corrosion resistance and surface quality in aerospace components․ Compliance with its specifications guarantees reliability, safety, and performance in critical applications worldwide․
11․1 Summary of AMS2700E Importance
AMS2700E is a cornerstone for ensuring corrosion resistance and surface quality in aerospace components․ Its specifications guarantee the removal of contaminants, enhancing durability and reliability․ By standardizing passivation processes, it maintains consistency across manufacturing, critical for safety and performance․ Compliance with ASTM A967 further underscores its credibility․ AMS2700E’s focus on citric acid passivation aligns with modern environmental and safety standards, making it indispensable for the aerospace industry’s high-performance requirements․
11․2 Final Thoughts on Implementation and Compliance
Implementation of AMS2700E requires strict adherence to its guidelines to ensure optimal corrosion resistance and surface quality․ Manufacturers must prioritize proper passivation processes, leveraging citric acid for environmental safety․ Compliance not only meets aerospace standards but also enhances component reliability․ Regular updates to the specification highlight the need for ongoing education and adaptation․ By aligning with AMS2700E, industries can achieve both performance excellence and cost efficiency, solidifying its role as a critical standard in modern aerospace manufacturing․